The host factory for this BasePower project produces filled pastry products for large food retailers and is part of a group with multiple production sites across the UK.
The Imperative to Use Less Energy
With a growing presence in the highly competitive food industry, this client wanted to find ways to reduce energy use and costs while also improving sustainability.
Firstly, the BasePower team conducted a detailed analysis of the site’s energy usage data. We then worked alongside the site’s Procurement and Engineering teams to produce a feasibility study for an on-site Combined Heat and Power (CHP) scheme and a replacement main boiler, to be financed, built, and operated by BasePower. This project proposal was subsequently approved by the Board.
BasePower developed, built and now operates the promised energy centre, which converts grid gas into 24-hour electricity, steam and hot water for use around the site.
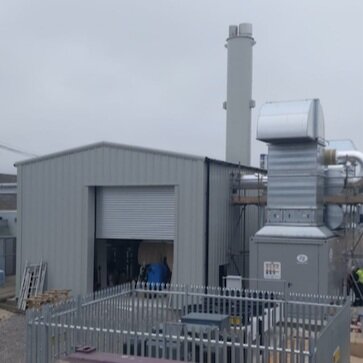
Project Overview
The outbreak of the Covid-19 pandemic shortly after construction began in March 2020 caused unprecedented risk and supplier management challenges, limiting the BasePower team to working remotely at times. Following immediate implementation of Covid-secure measures the client was happy for the project to continue, with minimal impact on the programme.
A 1.3MW MTU engine supplied by 2G was selected due to its ability to optimise high-efficiency generation at this size. Procurement of gas fuel for the engine is controlled by the client, allowing higher overall savings.
As an integral part of the project BasePower also upgraded the client’s existing boiler infrastructure. A dedicated dual-fired Byworth boiler was specified and fitted into a purpose-built boiler house on the site, both of which were procured by BasePower. Now the site’s mission-critical lead boiler and run by the client’s operating team, this prioritises heat from the CHP to make steam, with additional steam provided by grid gas when needed. Additional site loads requiring heat at below boiling point are provided via the engine’s cooling system.
Engine load and performance data from the Energy Centre can be viewed online on a real time basis. This allows BasePower and its key suppliers to respond proactively to any issues that might arise on a daily basis. The client is able to measure and manage its improved energy use.
Operational and Strategic Benefits
“Despite the Covid-19 outbreak causing some of the biggest construction challenges we have faced to date, this did not significantly delay the completion of the project which was designed and delivered within less than a year and is already reducing the client’s energy costs.”
Sacha Grodzinski, Construction Director, BasePower
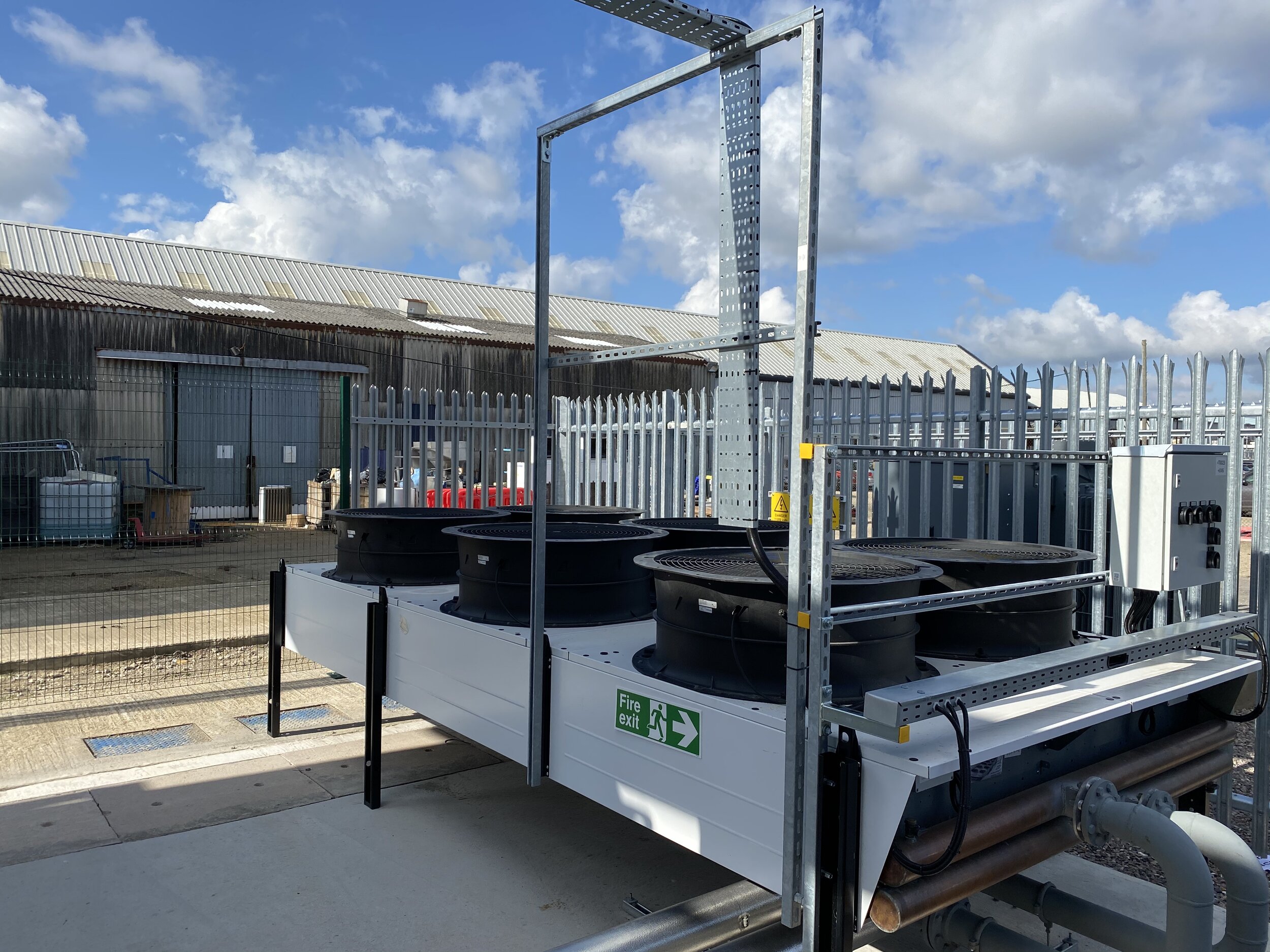
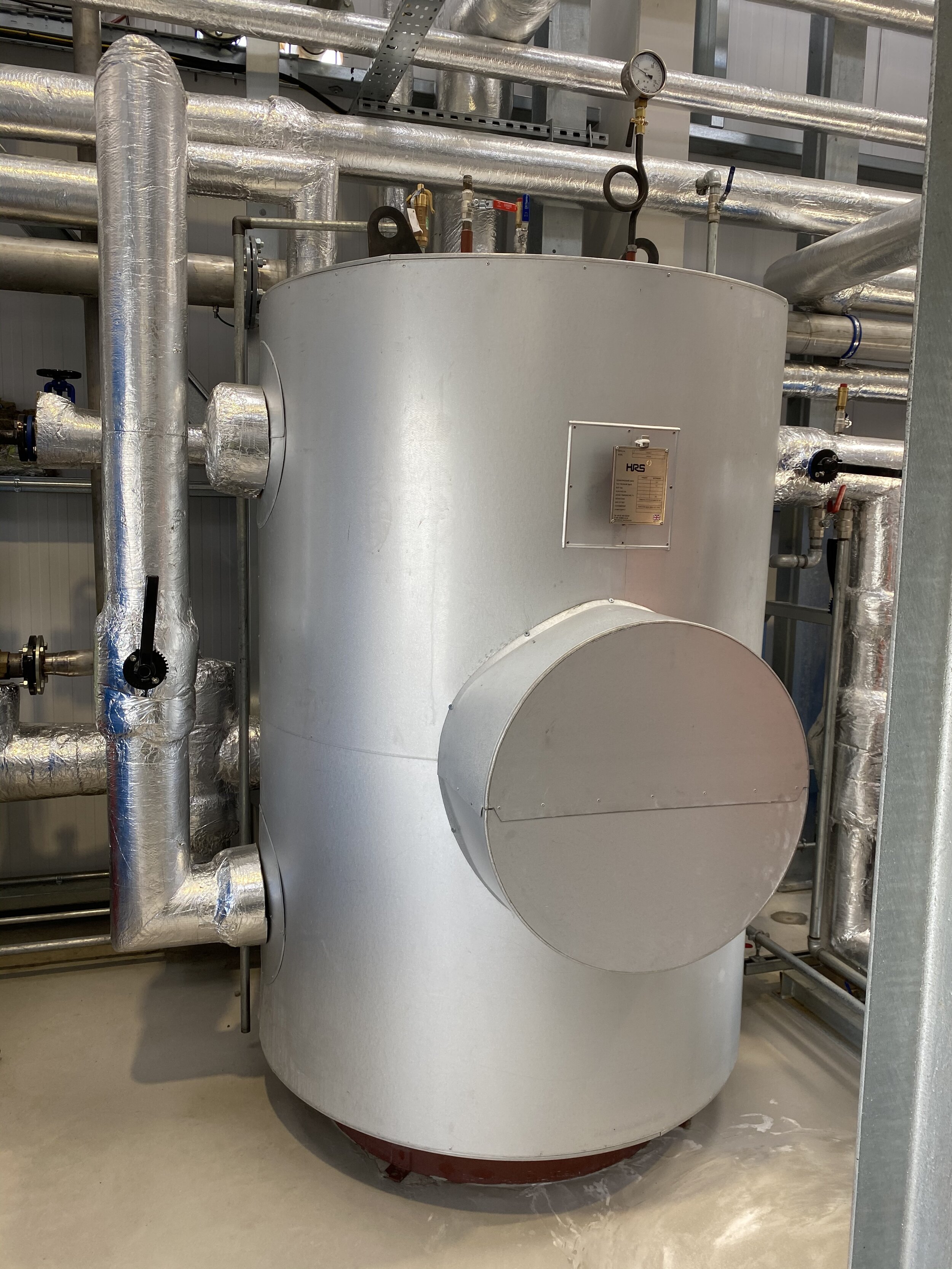
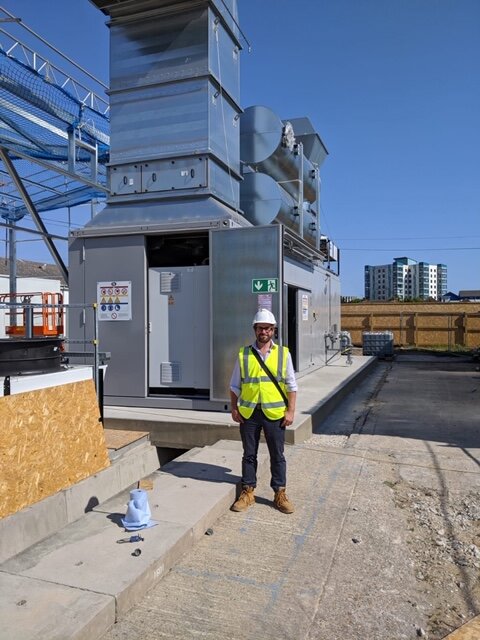
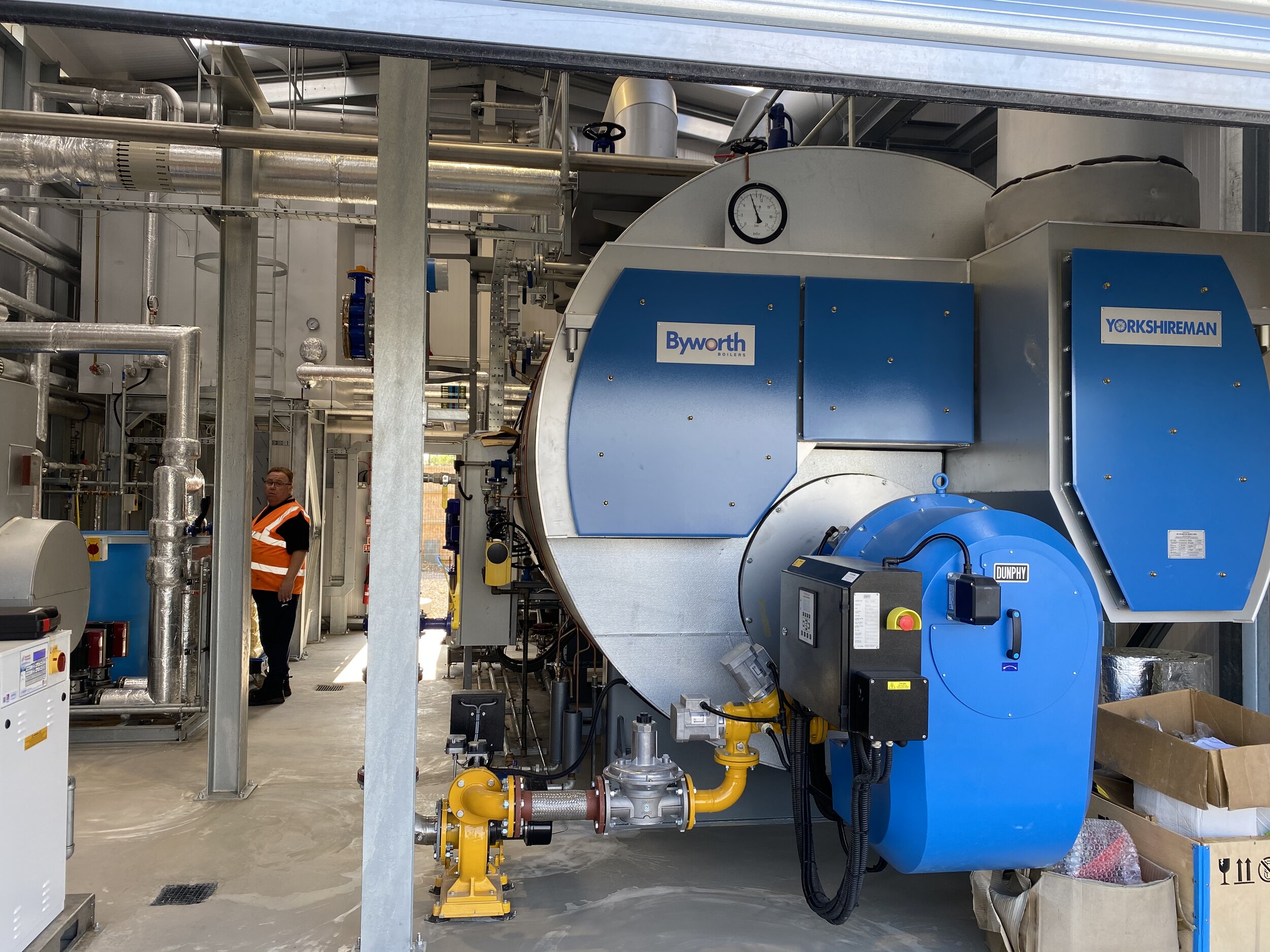
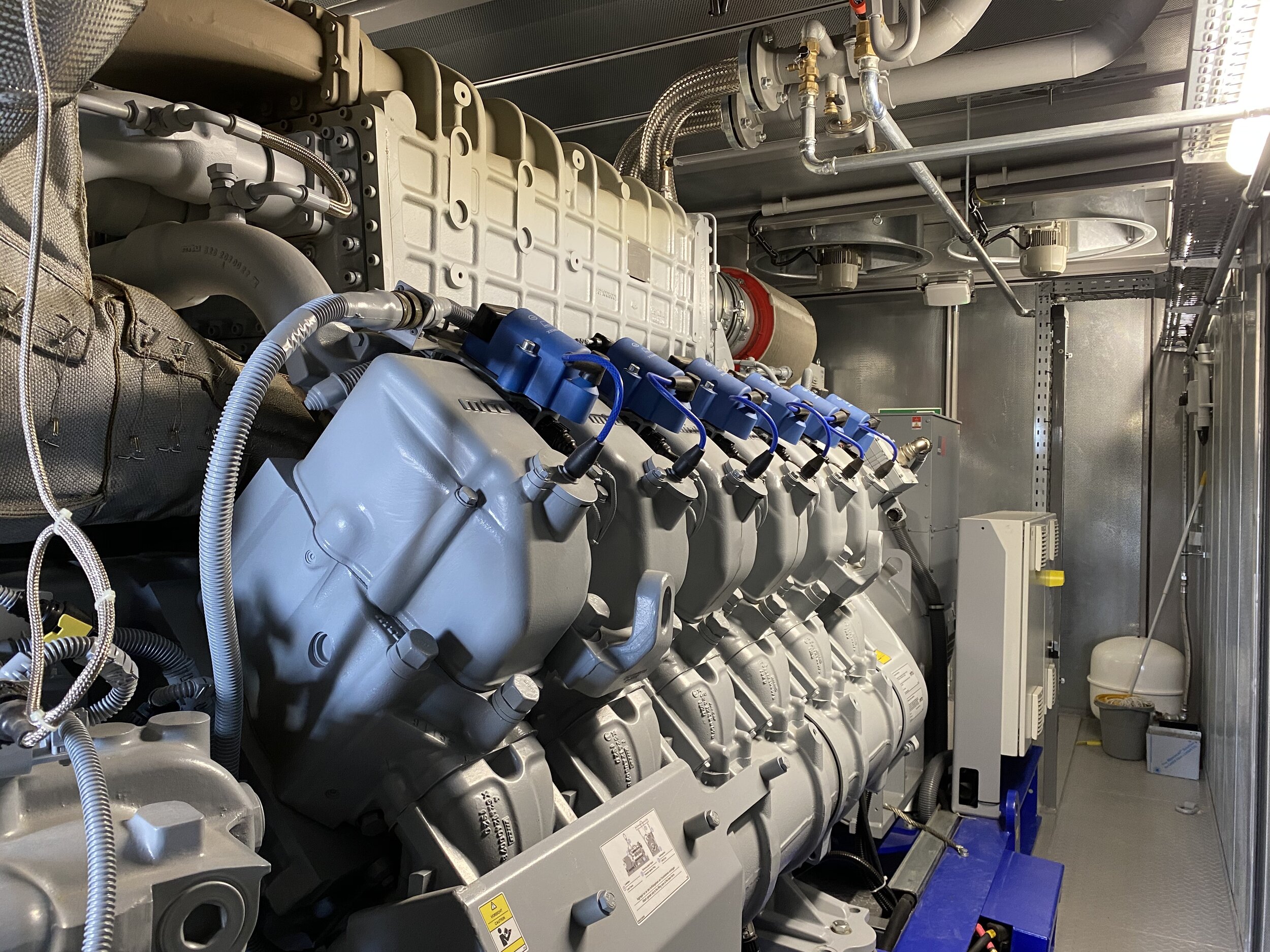
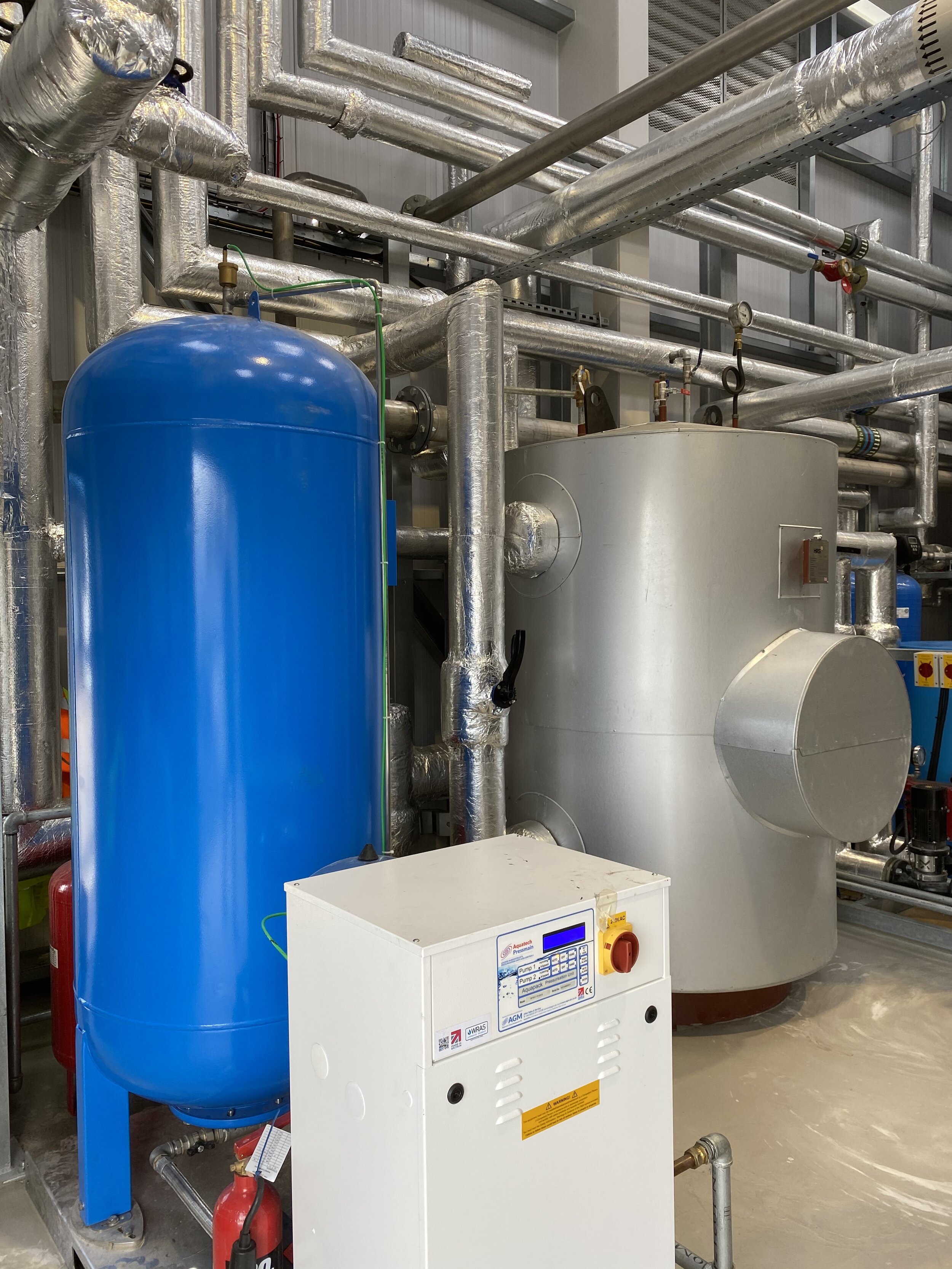
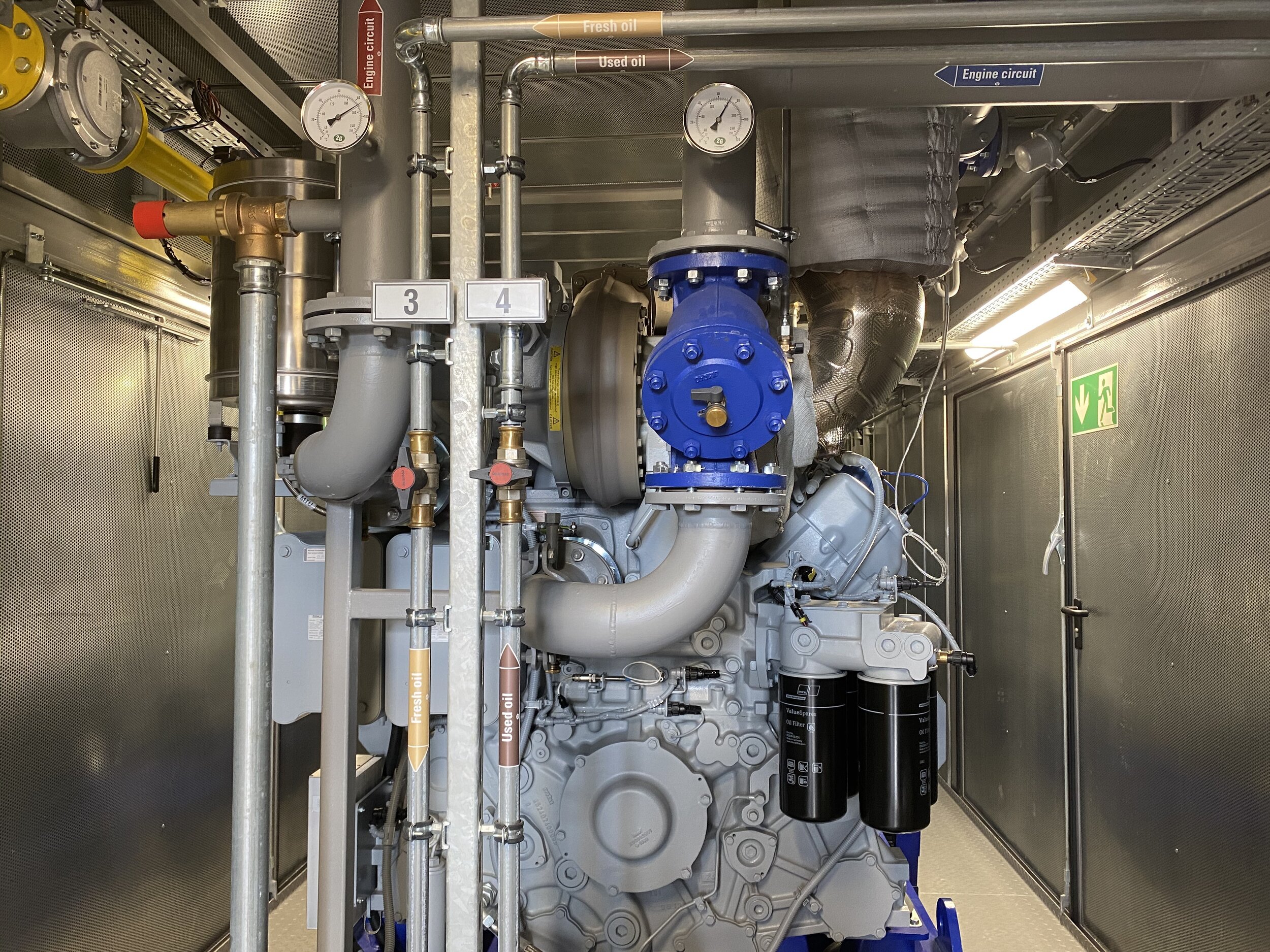
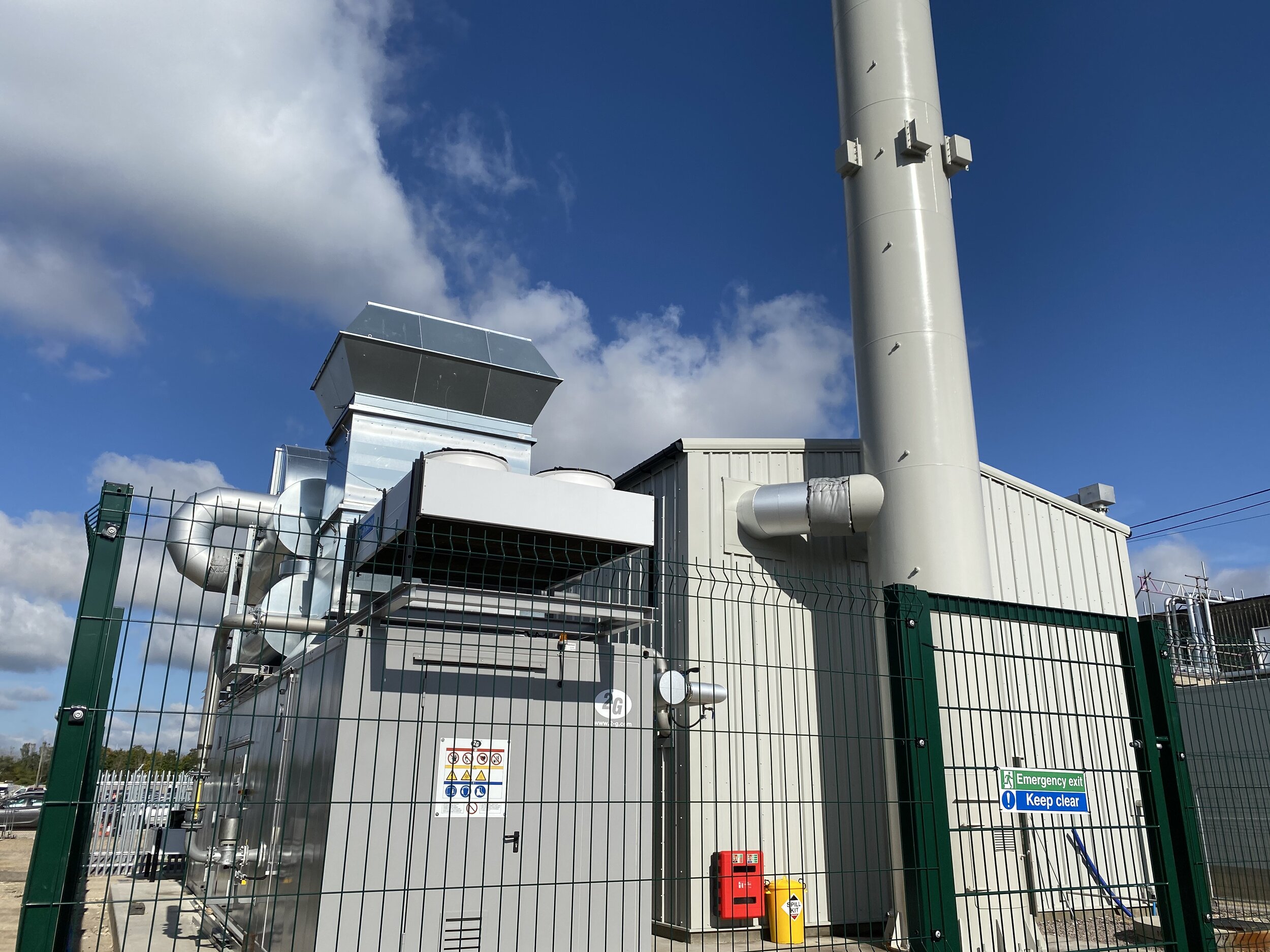
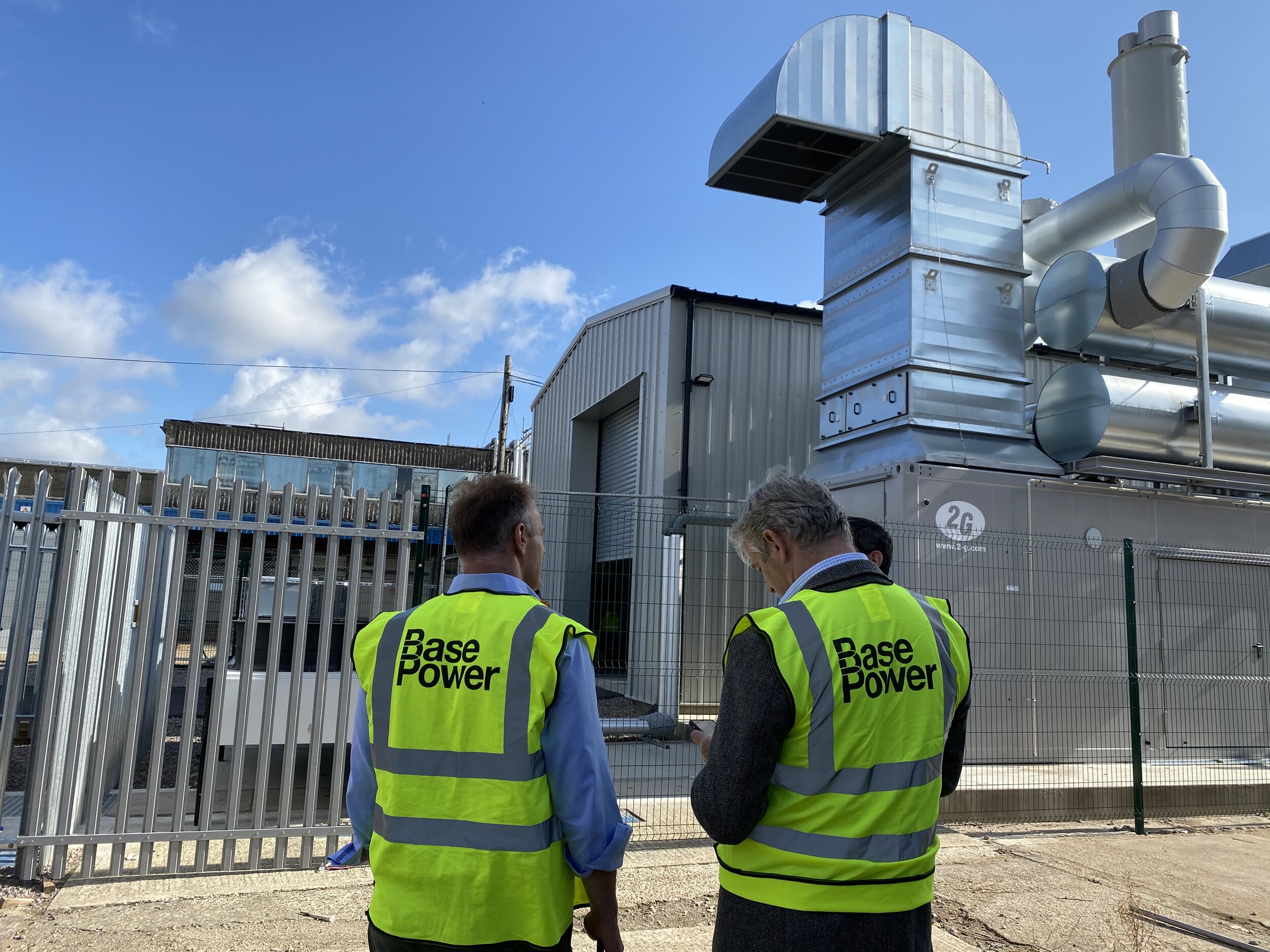
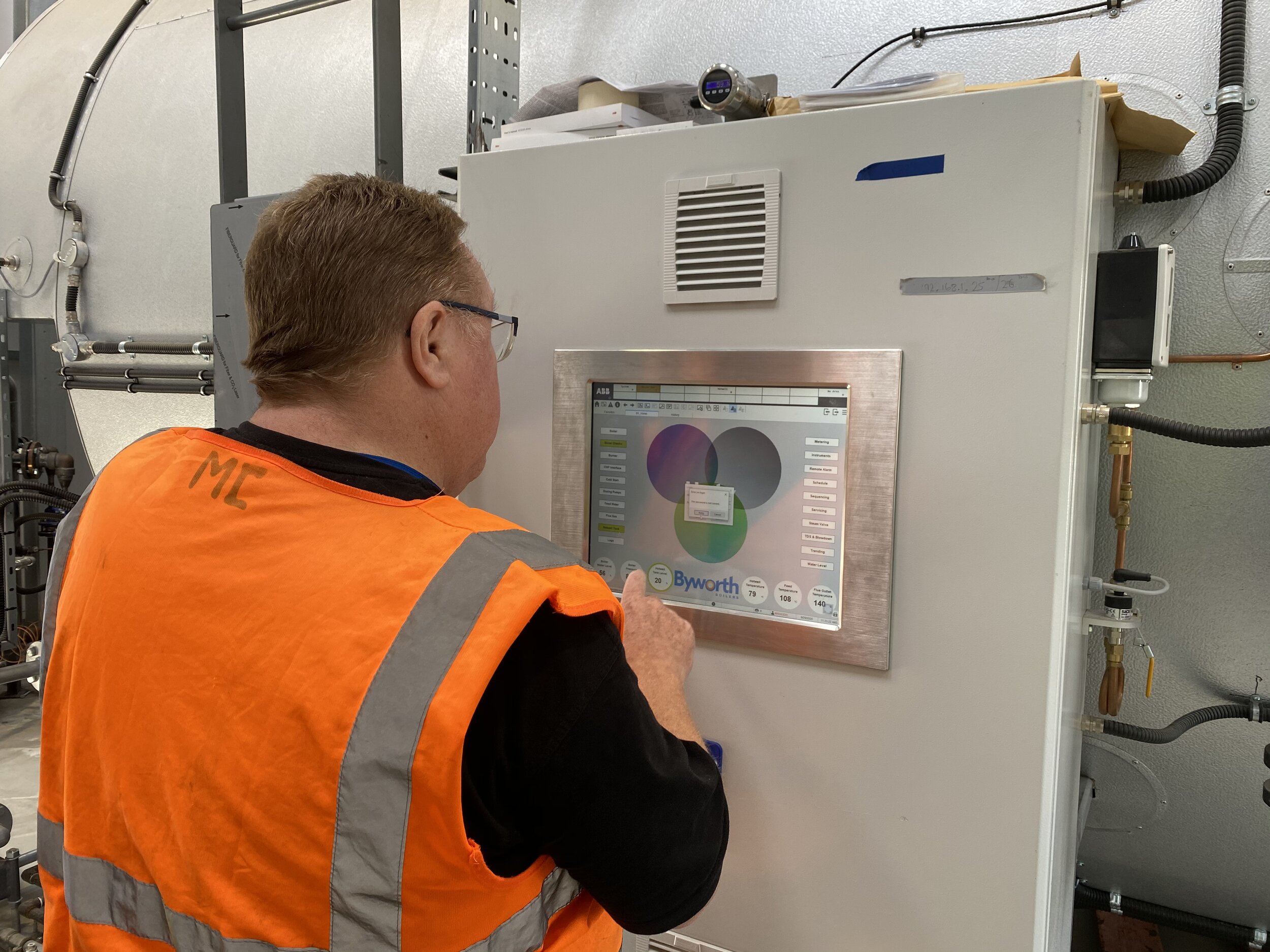
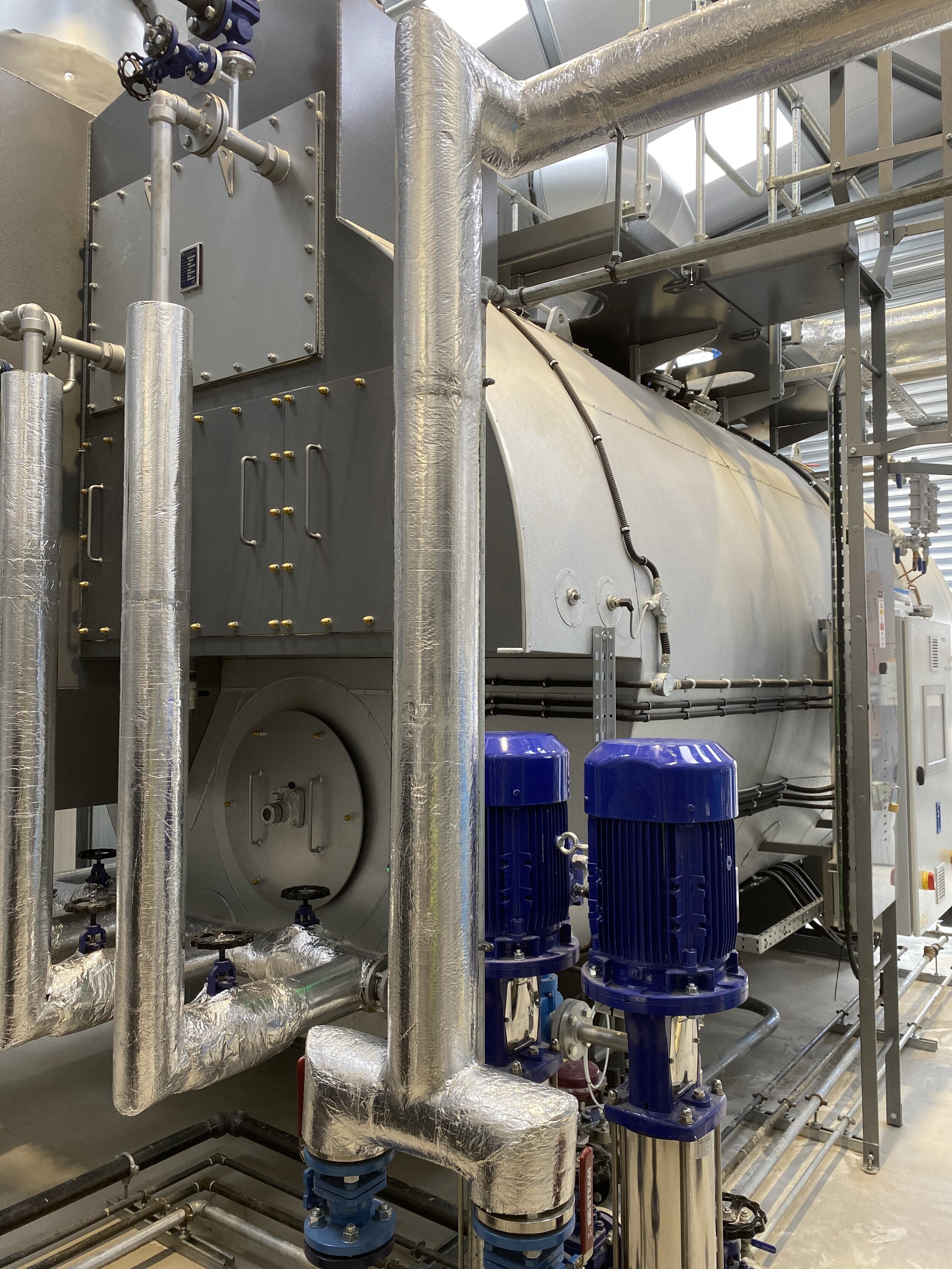
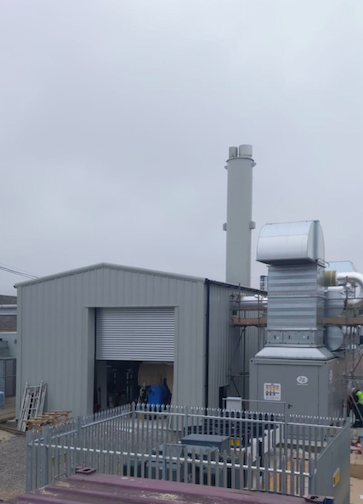
The Energy centre has been live since the summer of 2020.
The scheme has reduced the client’s energy bills, boosting overall business competitiveness
Energy efficiency has been optimised through a state of the art, more resilient boiler and hot water system
The project is forecast to save 340 tons of carbon per year and is a key driver towards the client’s sustainability goals.