This multi-national food company produces well-known heritage brands and private label products for the grocery sector. BasePower developed a project to upgrade the heat system at its largest manufacturing site, helping the client to reduce energy use and 1000t/y scope 1 Co2 emissions.
The BasePower Solution
The site is a heavy user of its legacy steam plant and has a Combined Heat and Power (CHP) scheme in operation, installed by a third party.
Through a brief submetering campaign, BasePower was able to identify several opportunities to desteam its processes and improve heat efficiency, all using ‘free’ heat from the CHP and other sources.
By installing a 2MW hot water distribution ring which initially takes its heat from the CHP, the BasePower intervention will improve the site’s CIP effectiveness and cycle time while reducing energy usage equivalent to 1,000t/y of Scope 1 CO2.
A second phase will extend the heat recovery to waste condensate and a refurbished economiser, supplying this (via the Phase 1 distribution ring) for the preheat and temperature maintenance of liquid ingredients. This will drive further financial and CO2 savings as well as additional cycle time improvement.
The payback for Phase 1 of the project will be as little as two years. The Capex is supplied by the site.

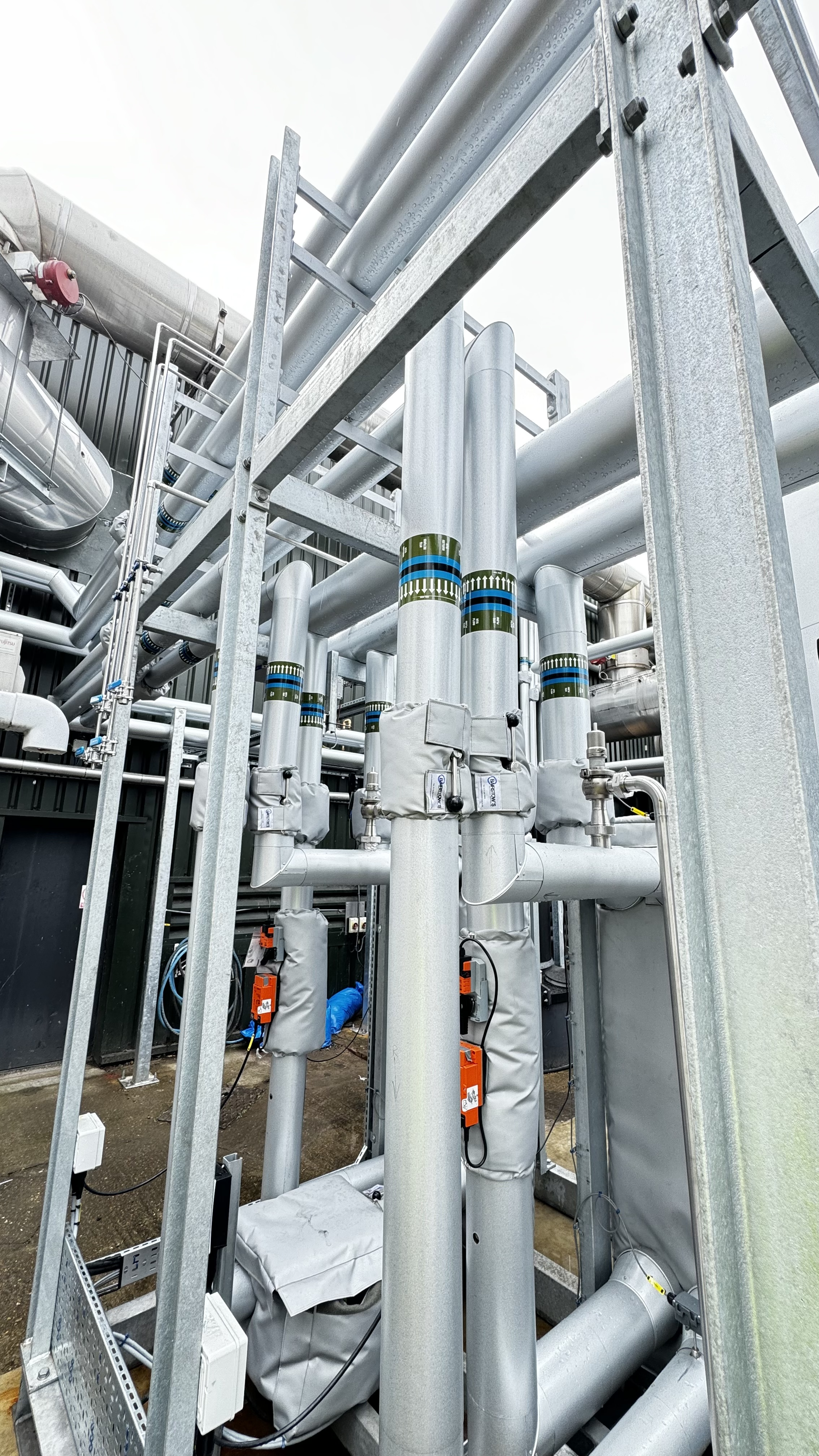
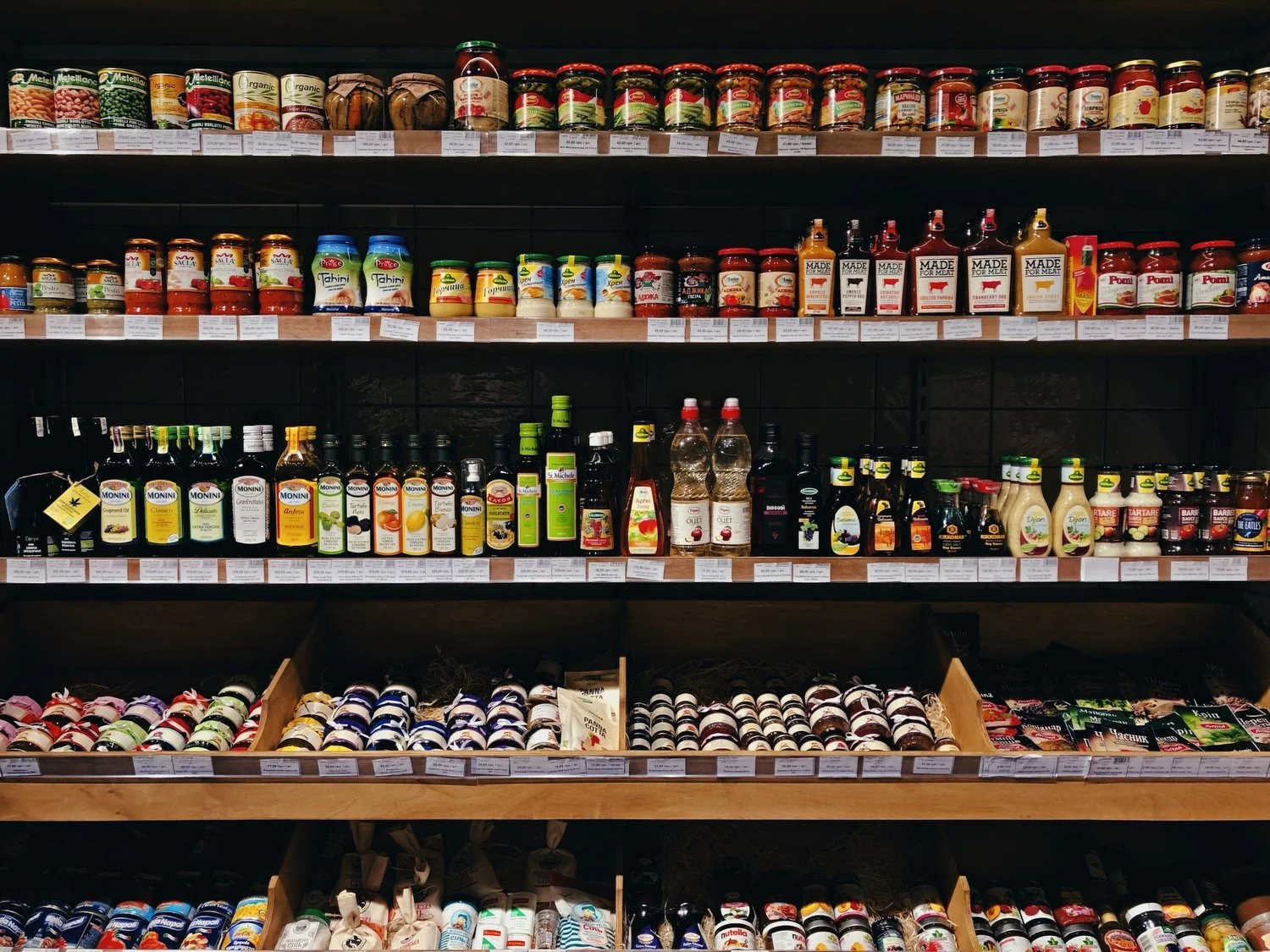